In the ever-evolving landscape of industrial manufacturing, robotics has emerged as a cornerstone of innovation, driving efficiency, precision, and productivity to unprecedented heights. The integration of robotics into industrial processes is not just transforming production lines but also redefining the very essence of modern manufacturing. This article delves into the latest innovations in robotics that are optimizing production processes, exploring how these advancements are reshaping industries and creating new benchmarks for operational excellence.
1. Collaborative Robots (Cobots)
One of the most significant advancements in industrial robotics is the development of collaborative robots, or cobots. Unlike traditional industrial robots that operate in isolation, cobots are designed to work alongside human workers, enhancing productivity and safety. Equipped with advanced sensors, machine learning algorithms, and AI, cobots can perform complex tasks with high precision while ensuring a safe working environment.
1.1 Enhanced Human-Robot Interaction
Cobots are programmed to understand and predict human actions, allowing for seamless collaboration on the factory floor. For instance, in automotive manufacturing, cobots assist in assembling intricate components, reducing the physical strain on workers and increasing overall efficiency. By taking over repetitive and strenuous tasks, cobots enable human workers to focus on more complex and creative aspects of production.
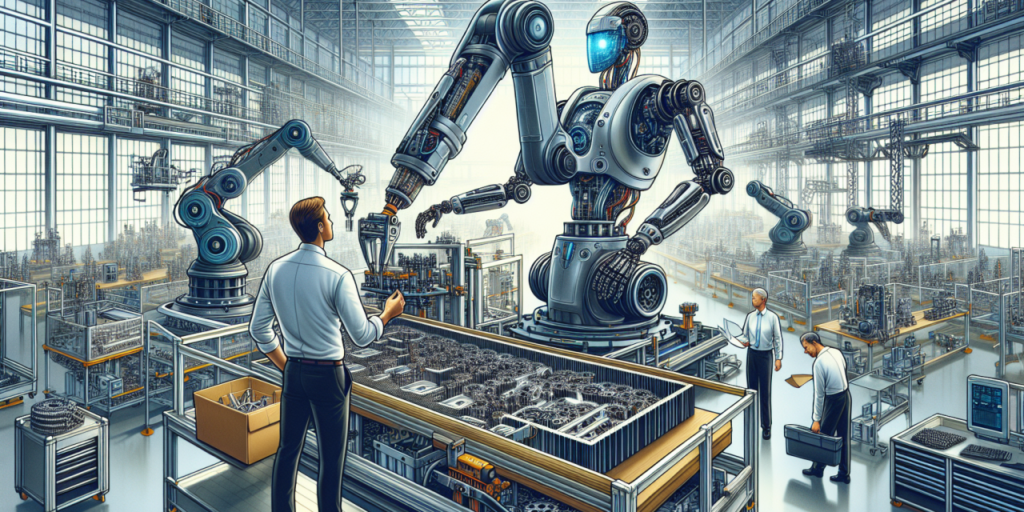
1.2 Safety and Flexibility
Modern cobots are equipped with sophisticated safety features, including force sensing and emergency stop capabilities, ensuring they can operate safely alongside humans. Their flexibility and ease of programming make them ideal for small and medium-sized enterprises (SMEs) looking to enhance productivity without extensive reconfiguration of their existing workflows.
2. Autonomous Mobile Robots (AMRs)
Autonomous Mobile Robots (AMRs) represent a leap forward in intralogistics, automating the transportation of materials within manufacturing facilities. Unlike traditional Automated Guided Vehicles (AGVs), which require predefined paths and physical guides, AMRs utilize advanced navigation systems, such as LiDAR and computer vision, to navigate dynamically through complex environments.
2.1 Dynamic Pathfinding and Navigation
AMRs can adapt to changing conditions on the factory floor, finding optimal paths and avoiding obstacles in real-time. This adaptability is crucial in industries with high variability in workflows, such as electronics manufacturing, where components and products move frequently between different production stations.
2.2 Integration with IoT and AI
Integration with the Internet of Things (IoT) and AI enhances the capabilities of AMRs, enabling real-time data exchange and decision-making. For example, an AMR can communicate with warehouse management systems (WMS) to prioritize tasks, optimize routes, and ensure timely delivery of materials, thereby reducing downtime and increasing throughput.
3. Robotic Process Automation (RPA)
Robotic Process Automation (RPA) extends the concept of robotics beyond physical tasks to automate digital processes. RPA involves the use of software robots, or “bots,” to automate repetitive and rule-based tasks in industries such as finance, healthcare, and manufacturing.
3.1 Streamlining Administrative Tasks
In manufacturing, RPA can automate administrative tasks such as order processing, inventory management, and compliance reporting. By automating these processes, companies can reduce human error, speed up operations, and free up employees to focus on higher-value tasks.
3.2 Enhanced Data Analytics
RPA bots can also collect and analyze data from various sources, providing actionable insights for decision-making. For example, in quality control, RPA can aggregate data from different inspection points and identify patterns or anomalies, enabling proactive measures to maintain product standards.
4. Advanced Robotics in Quality Control
Quality control is a critical aspect of manufacturing, and advancements in robotics are enhancing the accuracy and efficiency of quality inspection processes. Robotic vision systems, powered by AI and machine learning, are capable of detecting defects with greater precision than human inspectors.
4.1 Machine Vision and Deep Learning
Robotic systems equipped with machine vision use high-resolution cameras and deep learning algorithms to inspect products for defects such as scratches, dents, or misalignments. These systems can learn and improve over time, continuously refining their inspection criteria and reducing the rate of false positives and negatives.
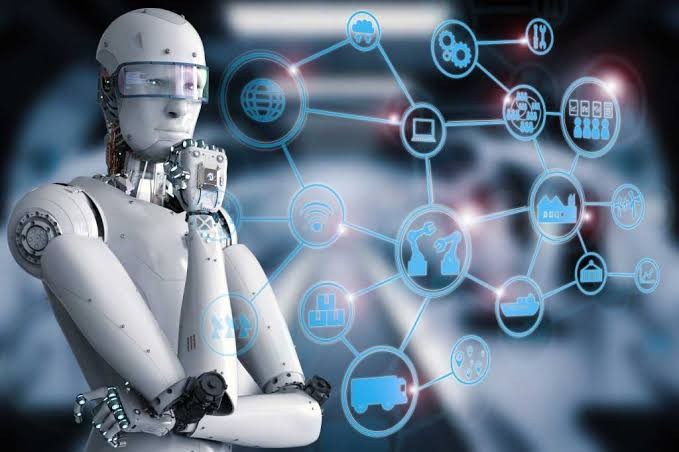
4.2 Non-Destructive Testing (NDT)
Advanced robotics are also employed in non-destructive testing (NDT) methods, such as ultrasonic and X-ray inspections, to assess the integrity of materials and components without causing damage. For instance, in aerospace manufacturing, robotic NDT systems ensure the structural integrity of aircraft parts, enhancing safety and reliability.
5. Robotic Welding and Fabrication
Welding and fabrication are labor-intensive processes that benefit significantly from robotic automation. Robotic welding systems deliver consistent, high-quality welds with greater speed and precision than manual welding.
5.1 Precision and Consistency
Robotic welders can be programmed to perform intricate welding tasks with a high degree of accuracy, ensuring uniformity and strength in welds. This precision is particularly valuable in industries such as automotive and aerospace, where the quality of welds directly impacts the safety and performance of the final product.
5.2 Complex Fabrication
Advanced robotic fabrication systems can handle complex geometries and materials, enabling the production of components that would be challenging or impossible to fabricate manually. These systems use techniques such as additive manufacturing (3D printing) and laser cutting to create detailed and customized parts.
6. Smart Factories and Industry 4.0
The concept of Industry 4.0 encompasses the integration of robotics, IoT, AI, and big data to create smart factories. These factories operate with a high level of automation, connectivity, and data-driven decision-making.
6.1 Predictive Maintenance
In smart factories, robotic systems are equipped with sensors that continuously monitor their performance and condition. Predictive maintenance algorithms analyze this data to predict potential failures and schedule maintenance activities proactively. This approach minimizes downtime, extends the lifespan of equipment, and reduces maintenance costs.
6.2 Digital Twins
Digital twins are virtual replicas of physical assets, processes, or systems that use real-time data to simulate and optimize operations. In manufacturing, digital twins can model production lines, predict the impact of changes, and optimize workflows. By integrating digital twins with robotic systems, manufacturers can enhance efficiency, reduce waste, and improve product quality.
7. The Future of Robotics in Industry
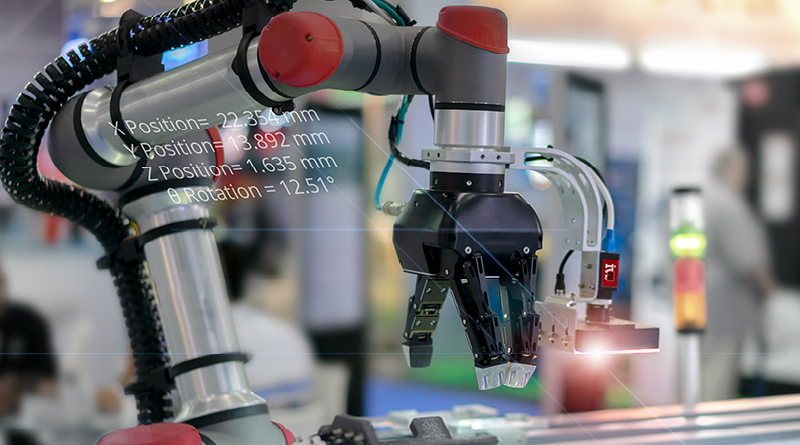
The future of industrial robotics holds exciting possibilities, driven by ongoing advancements in AI, machine learning, and materials science. Emerging trends include the development of soft robotics, which mimic the flexibility and dexterity of human hands, and swarm robotics, where multiple robots collaborate to perform complex tasks.
7.1 Soft Robotics
Soft robotics, made from flexible and compliant materials, can handle delicate objects and perform tasks that require a gentle touch. These robots have potential applications in industries such as electronics and food processing, where precision and care are paramount.
7.2 Swarm Robotics
Swarm robotics involves coordinating multiple robots to work together as a cohesive unit. Inspired by natural systems such as ant colonies and bird flocks, swarm robots can perform tasks such as assembly, logistics, and exploration more efficiently than single robots. This approach offers scalability and redundancy, enhancing resilience in industrial operations.
Robotics in industry is not just about automation; it is about creating smarter, more efficient, and more adaptable production processes. Innovations in collaborative robots, autonomous mobile robots, robotic process automation, advanced quality control, robotic welding and fabrication, and smart factories are driving this transformation. As these technologies continue to evolve, they will unlock new levels of productivity, quality, and sustainability, shaping the future of manufacturing and setting new standards for operational excellence. The integration of robotics into industrial processes marks the dawn of a new era in manufacturing, where human ingenuity and robotic precision work hand in hand to achieve unprecedented heights.